Conventional Lithium Extraction
Frantic Hunt for Lithium
Lithium, an integral ingredient in EV batteries and energy storage, is gradually taking over petroleum and natural gas as the critical commodity for the ongoing green energy revolution. All battery chemistries (NMC, LFP, solid state, silicon anodes, etc.) require lithium as the key element, with lithium demand projected to increase by >10x in 2040 relative to today.
Despite tens of billions in capital expenditure pouring into lithium mineral exploration and development, minable lithium reserves and resources are falling short of projected industrial demand, underscoring the need for a dramatic breakthrough in mining and refining technology.
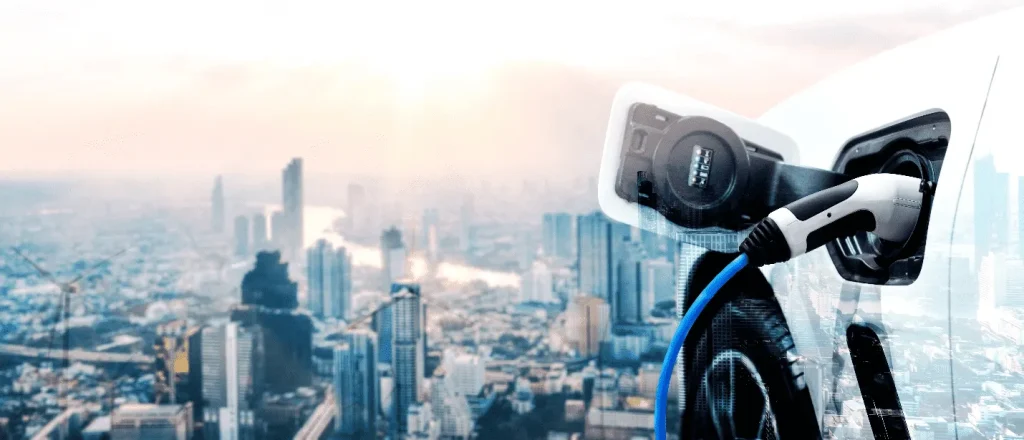
The Lithium Paradox
Despite paving the way for a greener future, conventional methods of lithium extraction, such as hardrock mining and salt lake mining, inevitably harm the environment in the form of soil degradation, biodiversity loss, water contamination, and substantial greenhouse gas emissions .
A recent study by MIT revealed that the extraction of one tonne of lithium emits approximately 15 tonnes of CO2 into the atmosphere. It’s been further estimated that the carbon footprint of an electric vehicle is bigger than that of a gasoline car until one has driven at least 50,000 miles, due to emissions as a result of acquiring and processing primarily lithium.
Therefore, the advent of Direct Lithium Extraction (DLE) technologies has been hailed as a potential panacea. However, it is imperative to critically evaluate their true efficacy.
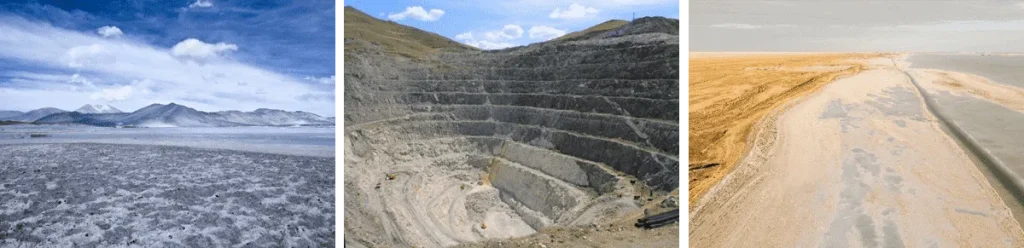
COMPETING DLE
DLE Claims
DLE technologies are often paraded to resolve the following issues that arise from conventional lithium brine extraction:
High Mg/Li Ratio
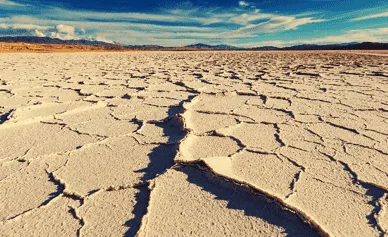
High Water Usage
Producing one tonne of lithium can require up to 70,000 liters of water, which creates irreversible ecological exhaustion and community disintegration
Long Production Timeframe
Conventional extraction through evaporation ponds alone can take up to two years
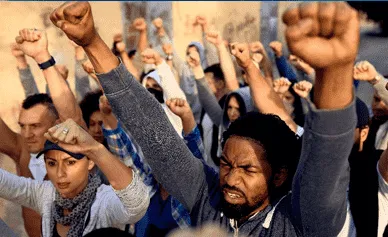
Low Yield
South American brine producers typically achieve yields of only 30-40% with the rest discarded, resulting in significant loss of valuable reserve
DLE Methodologies
Promising DLE technologies are currently being developed not only by emergeing tech-savvy players but also by companies who wish to optimize traditional brine assets. DLE technologies can generally be classified into four broad categories, though some adopt a combined approach:
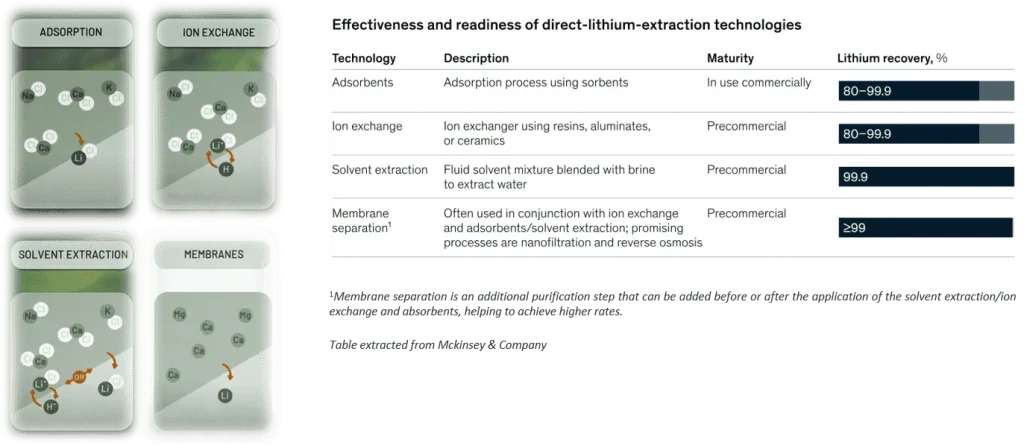
The DLE Reality
DLE companies often self-claim to be able to solve all four abovementioned issues, but in reality, we witness these prevailing technologies having one or more shortcomings:
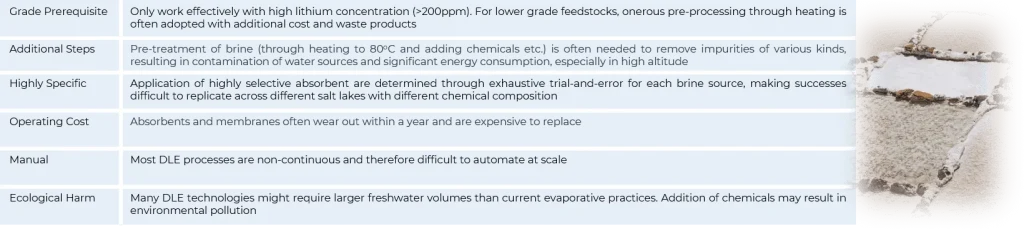
Therefore, successful DLE stories are often sporadic small-scale LCE production on salt lakes previously impossible to produce, or marginal improvements to supplement existing evaporation pond operations.
Not surprisingly, we are yet to witness any commercial success in processing Li brine feedstocks of <200ppm.
Lorem ipsum dolor sit amet, consectetur adipiscing elit. Ut elit tellus, luctus nec ullamcorper mattis, pulvinar dapibus leo.
Our Approach
The Poorest Feedstock, with the Simplest Process
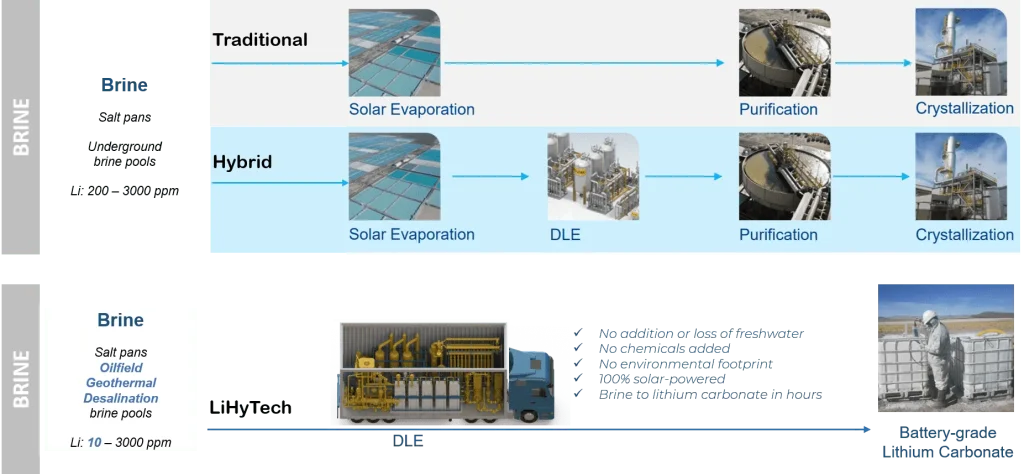
A New World of Infinite Lithium Supply
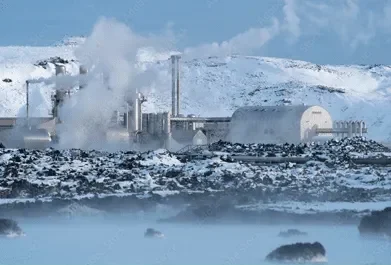
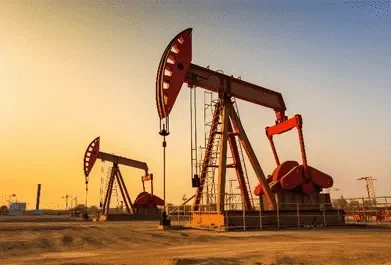
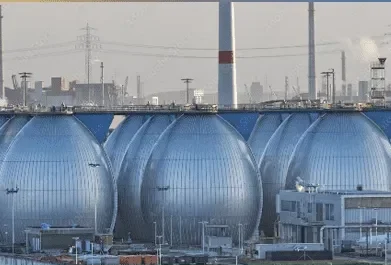
Existing documented lithium reserves of 20 million tonnes, with current extraction yields of less than 50%, imply that global lithium reserves could be depleted sooner than expected. Our ability to economically extract lithium from low-grade geothermal and oilfield brines opens a new world of lithium resource, with production cost sitting comfortably between 1st – 2nd quartile of global lithium cost curve, depending on the grade of the brine feedstock.
It is estimated that > 10 billion tonnes of produced water from oilfields available per annum1, with concentration ranging from 10-200ppm of Li confirmed in USGS and GLJ publications. We are testing samples provided to us by a major energy producer, which confirms reasonably high lithium and low magnesium content suitable for LiHyTech extraction. Without a single dollar of capex going into drilling, 10 billion tonnes of oilfield brine translate to potentially ~2.5 million tonnes LCE of annual petrolithium production, assuming an average grade of 50ppm and 95% recovery. Many more suspended oilwells with high water-cut and high lithium content can be brought back to production solely to produce lithium, with little capital investment.
An additional >5 billion tonnes per annum of brine production from desalination and geothermal groundwater is extractable, with a majority of them in MENA region2. If fully utilized, would translate to another ~1 million tonnes of annual LCE production.
1. Produced water treatment technologies. International Journal of Low-Carbon Technologies (2012)
2. The state of desalination and brine production: A global outlook. Science of The Total Environment (2019)
The DLE Reality
DLE companies often self-claim to be able to solve all four abovementioned issues, but in reality, we witness these prevailing technologies having one or more shortcomings:
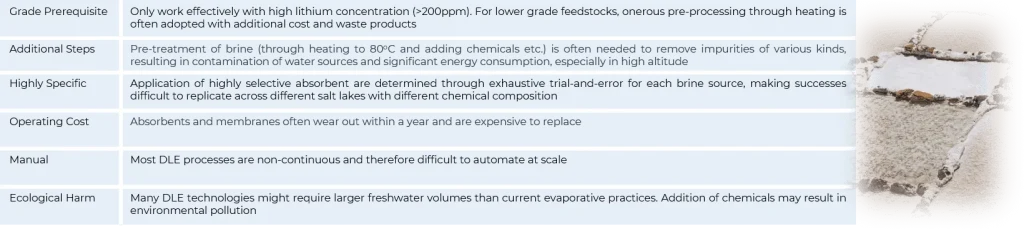
Therefore, successful DLE stories are often sporadic small-scale LCE production on salt lakes previously impossible to produce, or marginal improvements to supplement existing evaporation pond operations.
Not surprisingly, we are yet to witness any commercial success in processing Li brine feedstocks of <200ppm.
Lorem ipsum dolor sit amet, consectetur adipiscing elit. Ut elit tellus, luctus nec ullamcorper mattis, pulvinar dapibus leo.